Plastic extrusion used in building, automotive, and more
Plastic extrusion used in building, automotive, and more
Blog Article
A Comprehensive Guide to the Process and Benefits of Plastic Extrusion
In the substantial realm of manufacturing, plastic extrusion arises as a necessary and very efficient process. Translating raw plastic into constant accounts, it provides to a huge selection of industries with its amazing adaptability.
Understanding the Fundamentals of Plastic Extrusion
While it may appear complex at first look, the process of plastic extrusion is essentially basic. The procedure starts with the feeding of plastic product, in the type of pellets, powders, or granules, into a heated barrel. The shaped plastic is after that cooled, solidified, and cut into desired lengths, completing the procedure.
The Technical Process of Plastic Extrusion Explained
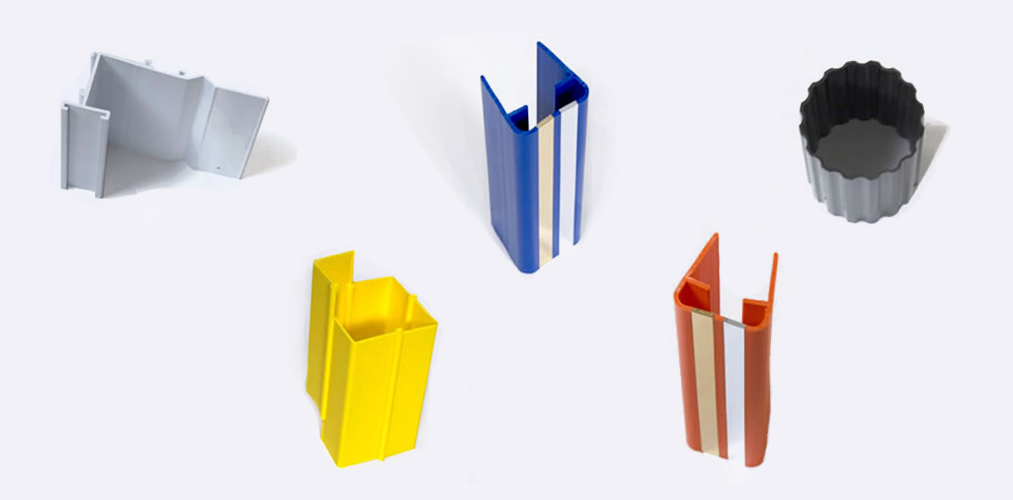
Kinds Of Plastic Suitable for Extrusion
The selection of the best kind of plastic is an important aspect of the extrusion process. Different plastics supply unique homes, making them more suited to certain applications. Polyethylene, for instance, is commonly utilized because of its reduced cost and simple formability. It uses superb resistance to chemicals and dampness, making it perfect for items like tubes and containers. Likewise, polypropylene is one more preferred choice due to its high melting point and resistance to fatigue. For even more robust applications, polystyrene and PVC (polyvinyl chloride) are frequently chosen for their stamina and durability. Although these are common options, the selection eventually relies on the certain demands of the product being created. Comprehending these plastic types can dramatically improve the extrusion process.
Comparing Plastic Extrusion to Various Other Plastic Forming Methods
Understanding the kinds of plastic appropriate for extrusion leads the way for a wider conversation on how plastic extrusion piles up against other plastic creating methods. These consist of shot molding, impact molding, and thermoforming. Each technique has its unique usages and advantages. Shot molding, for instance, is exceptional for producing intricate components, while impact molding is ideal for hollow objects like containers. Thermoforming excels at forming superficial or big components. Plastic extrusion is unequaled when it comes to producing continuous profiles, such as seals, gaskets, and pipelines. It also enables a constant cross-section along the size of the item. Thus, the selection of method mostly depends upon the end-product requirements and specs.
Key Benefits of Plastic Extrusion in Production
In the realm of production, plastic extrusion uses many substantial advantages. One notable benefit is the cost-effectiveness of the procedure, which makes it an economically appealing manufacturing approach. Additionally, this technique provides superior item flexibility and enhanced production speed, therefore increasing overall production efficiency.
Cost-efficient Production Method
Plastic extrusion leaps to the forefront as a cost-effective production method in production. Additionally, plastic extrusion requires less power than traditional manufacturing techniques, contributing to reduced operational expenses. On browse around these guys the whole, the economic benefits make plastic extrusion a very eye-catching alternative in the production market.

Superior Product Adaptability
Beyond the cost-effectiveness of plastic extrusion, one more significant benefit in manufacturing lies in its remarkable item flexibility. This makes plastic extrusion an excellent option for industries that require personalized plastic elements, such as automobile, building, and product packaging. In significance, plastic extrusion's product adaptability fosters development while improving operational effectiveness.
Boosted Manufacturing Rate
A substantial benefit of plastic extrusion lies in its boosted manufacturing speed. This production procedure allows for high-volume production in a reasonably brief time period. It is qualified of generating long, continuous plastic profiles, which substantially minimizes the production time. This high-speed manufacturing is especially helpful in industries where big quantities of plastic components are required within limited target dates. Couple of other production procedures can match the speed of plastic extrusion. In addition, the ability to maintain regular high-speed production without compromising item high quality establishes plastic extrusion apart from other techniques. The improved production you could look here rate, as a result, not just allows makers to meet high-demand orders however also adds to enhanced efficiency and cost-effectiveness. This beneficial attribute of plastic extrusion has made it a recommended choice in many markets.
Real-world Applications and Effects of Plastic Extrusion
In the world of production, the strategy of plastic extrusion holds extensive importance. This process is extensively utilized in the manufacturing of a variety of items, such as plastic tubing, home window structures, and weather condition stripping. As a result, it significantly affects markets like building, packaging, and automotive markets. Furthermore, its effect encompasses day-to-day items, from plastic bags to tooth brushes and disposable cutlery. The economic advantage of plastic extrusion, largely its cost-effective and high-volume output, has transformed manufacturing. The ecological impact of plastic waste stays a problem. For that reason, the industry is persistently pursuing innovations in naturally degradable and recyclable products, indicating a blog here future where the advantages of plastic extrusion can be maintained without endangering ecological sustainability.
Conclusion
Finally, plastic extrusion is a extremely reliable and reliable technique of changing raw products into diverse items. It offers numerous benefits over various other plastic creating methods, consisting of cost-effectiveness, high outcome, minimal waste, and style flexibility. Its effect is exceptionally felt in various sectors such as building and construction, vehicle, and durable goods, making it a critical process in today's production landscape.
Digging much deeper right into the technical process of plastic extrusion, it begins with the option of the suitable plastic material. As soon as cooled, the plastic is cut into the called for lengths or injury onto reels if the item is a plastic movie or sheet - plastic extrusion. Comparing Plastic Extrusion to Various Other Plastic Forming Techniques
Understanding the types of plastic ideal for extrusion paves the means for a wider conversation on how plastic extrusion piles up against other plastic developing methods. Couple of other manufacturing procedures can match the rate of plastic extrusion.
Report this page